The Textile Engineering & Instrumentation Division offers the following services.
1. Comprehensive Energy Audit
Conservation and management of energy have assumed tremendous significance in the last decade. SITRA has been conducting different types of energy audits like Comprehensive Energy Audit, BEE Mandatory Energy Audit and BEE Monitoring and Verification (M&V) Audit in the textile mills in India and abroad for more than four decades.
SITRA Energy Cell formed in 1980s, comprising of experienced engineers in the respective fields, is under taking Energy audits and energy consumption, conservation studies in the textile mills from powerhouse to production machines. So far, it has undertaken energy audits in about 650 mills in India and abroad. SITRA has also formulated procedures and systems for the introduction of Energy Conservation Program in mills for routine control and suggested methods to audit electrical energy consumption in mills. Many textile mills have saved crores of rupees in energy cost through SITRA Energy Audits. This audit is conducted in-depth in the following three areas:
Electrical Engineering
Auditing of electrical system infrastructure and review of energy monitoring systems of the mills – study of incoming (EHT/HT) supply quality and logging of load variations– study of inflow and outflow harmonics – power flow study –performance assessment of transformers–auditing of power distribution system (powerhouse) – inspection of in-house power generation facilities and their output measurements – study of neutral and earthling systems – performance appraisal of capacitors – cable loss estimation and measures for energy savings – study of hierarchical power factor and better solutions for “pf” improvement- evaluation of motor loading in ring frames, TFO, AWES, humidification system, Air-compressors –assessment of motor’s energy efficiency – lighting and illumination study.
Analysis of Power and demand (kVA) use- kWh and kVAh consumption analysis – mapping of productive, auxiliary and ancillary loads –suggestions for improving performance of electrical system – energy conservation measures in electrical systems and cost benefit analysis.
Mechanical Engineering
Humidification – system analysis for each department – supply, exhaust and pumping systems details – present condition of humidification system – air flow distribution analysis – heat load analysis – humidification power pattern – plant motor loading analysis – temperature and RH analysis – standard temperature and RH for different departments – plant operation and maintenance.
Compressors – power pattern – leakage analysis – boilers and thermic fluid heaters – existing system details – thermal efficiency analysis – recommendations for implementation.
Textile Engineering
Preparatory – Measurement of AWES suction pressure and waste levels in Blow room, carding and comber machines for optimisation, study to optimise the utilisation of Over Head Travelling Cleaners (OHTCs) and pneumafil motors in simplex machines, Study of work practices from energy conservation point of view, study of belt drives and inverter drives for conservation.
Spinning- Choice of energy efficient components or accessories: motors, bobbins, belts, spindles, spindle oils, spindle tapes, tin roller. Measurement of pneumafil and compact suction pressure for optimisation, energy saving in OHTCs, optimization of package size, cop content in ring frames – study of frame to frame variation in power consumption, modification in machine design or structure to reduce load, details of SITRA studies pertaining to energy conservation
Post-spinning machines – Measurement of yarn waste suction pressure for optimisation, study of utilisation of OHTCs and process parameters and study of link-coners for energy saving.
Mill SEC – Analysis of production and energy consumption for Mill’s existing specific energy consumption (SEC) assessment and formulation of target SEC and economics of using energy efficient equipment.
Conservation measures in weaving – Study of specific steam consumption in sizing, Study of expected air consumption in air-jet looms, OHTC utilisation and its pattern of use, machine to machine variation in power consumption, study of machine drives, fine tuning of weaving machines.
Conservation measures in wet processing – Study of specific electricity and steam consumption in wet processing machines in light, medium and dark shades. Scope for heat economy in processing machines.
2. BEE Mandatory Energy Audit
We are pleased to inform you that the Bureau of Energy Efficiency (BEE), Ministry of power, Government of India has approved SITRA to carry out BEE mandatory energy audit PAT Cycle. The details of the empanelment are available on BEE’s website www.bee-india.nic.in.
We are thankful to BEE for recognising SITRA’s expertise in the area of energy audits and its Energy cell comprising of experienced engineers in various disciplines such as Electrical, Mechanical and Textile engineering which has been offering these services since the 1980s. We hope to carry on the good work of the past 4 decades in the area of energy management through services like energy audits (more than 650 in India and abroad), energy conservation studies and training programmes.
3. BEE Monitoring & Verification (M&V)
We are pleased to inform you that the Bureau of Energy Efficiency (BEE), Ministry of power, Government of India has approved SITRA as an empanelled energy auditing firm to carry out Monitoring & Verification (M&V) under PAT Cycle, SITRA is exclusively empanelled to carry out Monitoring & Verification (M&V) only for the Textile sector under PAT Cycle III. The details of the empanelment are available on BEE’s website www.bee-india.nic.in.
We are thankful to BEE for recognising SITRA’s expertise in the area of energy audits and its Energy cell comprising of experienced engineers in various disciplines such as Electrical, Mechanical and Textile engineering which has been offering these services since the 1980s. We hope to carry on the good work of the past 4 decades in the area of energy management through services like energy audits (more than 1000 in India and abroad), energy conservation studies and training programmes.
4. Other Studies
Power Quality Audit
Study of parameters namely THD, “K” factor, cosφ and TPF, Hz, V, I, UbV, UbA(total harmonic distortions, “K” factor, displacement and true power factor, frequency, voltage, and current, capturing wave shape distortions, unbalance voltage and current) at vital nodes – power and harmonic flow study –– evaluation of kVAh and kWh consumption – study of harmonic impacts on transformers, motors, capacitors and cables.
PQ analytics – Evaluation of electrical failures and faults – a typical layout showing the best locations of harmonic filters and capacitors to maximizing filtering efficiency – PQ study suggestssuitable measures for reducing faults and cost of electricity, the methods and type of filters successful in culminating harmonic penalty, improving quality of power and performance of electrical system.
Humidification Study
Humidification is an important supportive activity for the production of yarns and fabrics. With reference to energy cost, it consumes nearly 15%-20% of the total power bill of the mill. SITRA has been conducting in-depth analysis on the humidification system of textile mills in the following aspects:
- Detailed heat load analysis in different departments.
- Plant capacity requirement with respect to supply, exhaust and pumping system.
- Design of the humidification plants.
- Design of the supply air ducts and diffusers.
- Design of the exhaust air trenches and floor grills.
- Pattern of temperature and humidity inside the departments.
- Loading of the motors in the humidification plants.
- Air distribution pattern inside the departments.
- Recommended lay-out for the supply and exhaust system for uniform distribution of air.
Compressed Air Audit
SITRA conducts detailed study on different types of compressors existing in the textile mills with respect to the following aspects:
- Air leakage study in the existing condition.
- Existing compressed air pipe line lay-out.
- Modified pipe line lay-out for minimum air friction loss.
- Selection of energy efficient compressed air accessories like filters, dryers and moisture separators.
- Compressed air for cleaning.
- Power consumption pattern of compressors.
Compressor Air Flow Measurement
Compressor Free Air Delivery is measured using flow sensors to know the compressor output Air. This measurement is used to find out the Specific energy consumption of the compressor in kw/cfm. This study helps the mill to identify the inefficient compressors.
Noise level study
Noise is often a problem in the working environment, whether from production machinery in the factory or business machines in the office. Noise measurement permits precise scientific analysis of annoying sounds. Noise level measurements give a clear indication of when a sound may cause hearing damage and permit corrective measures to be taken. Hence, measurement and analysis of sound is a powerful diagnostic tool in noise reduction programme. SITRA conducts detailed sound level analysis at different sections of a textile mill with sophisticated state-of-the-art instruments.
Mill UKG Assessment Study
Assessment of existing Ukg level in the mill is vital for ascertaining energy saving potential in mills. SITRA has developed standard procedure for calculating a spinning mill’s 40s converted Ukg using conversion factors and 4.10 Ukg in the present standard for single yarn production. Best mills are able to achieve a 40s adjusted Ukg below 3.8. This study will help the mill to standardize their Ukg assessment procedure for comparison with industry and SITRA standards and monitor and analyse periodic variation in mill values.
SITRA 40s UKG conversion factors are approved and adopted by Bureau of Energy Efficiency (BEE) for their ‘PAT’ scheme which is designed / promoted to enhance energy efficiency in individual spinning mills in the textile sector.
The accessories testing services offered by STIRA’s Textile engineering and instrumentation division provides end-to-end quality assurance solutions covering Testing solutions for the textile and allied industries. The highlight of SITRA’s services is its expertise, delivered consistently, with precision, pace and passion, enabling its customers to power ahead safely.
Testing of the accessories ensures that the risks are mitigated at every stage of development and manufacturing. From accessories such as paper cone, carton box, paper core and corrugated box components, enabling mills to deliver their core products to market with assurance. The accessories testing solutions encompass performance testing to measure torque, tension, compression, dimensional tolerances on nominal size, bridge deformation, material and surface quality, robustness etc.
The division, equipped with modern testing equipment, has exclusive facilities for testing of various textile ancillaries like rings, spindles, ring travelers, bottom and top rollers, meeting minimum requirements for performance and quality standards.
SITRA has been conducting the following tests for textile accessories as per the ISO requirements:
CARTON BOX / CORRUGATED BOX / KRAFTS SHEET
Bursting Strength, Edge Crushing Strength, Box Compression Strength, Puncture Resistant, Cobb Value, Bursting Factor, GSM, Thickness, Weight
Sample requirement : 1 Metre x 1 Metre
Box Compression Strength : Separate Box is needed
PAPER CONES
Cone Dimensions, Cone Eccentricity, Cone Crushing Strength, Cone Bursting Strength, Cone Weight
Sample requirement : Minimum 10 cones are required for each test
PAPER CORE
Core Crushing Strength
Sample requirement : Minimum 10 nos are required for each test
RINGS
Dimensional analysis, Hardness, Profile cutting & analysis, Traveller matching, Ring all tests.
Sample requirement : Minimum 5 rings are required for each test.
RING TRAVELLERS
Stretch test, Profile Analysis
SPINDLES
Dimensional analysis, Hardness of blade & bolster foot step bearing, Trueness of spindle, Tip wear
Sample requirement : Minimum 5 spindles are required
BOTTOM ROLLERS
Dimensional analysis, Hardness, Run-out, Breakage of flute
Sample requirement : Minimum 5 spindles are required
TOP ROLLERS
Dimensional analysis, Eccentricity, Shore hardness
Sample requirement : Minimum 5 rollers are required
RING FRAME TUBES & SIMPLEX BOBBINS
Dimensional analysis, Eccentricity
Sample requirement : Minimum 10 tubes / bobbins are required
CARDWIRE
Doffer, Cylinder & Licker-in profiles
ROVING BOBBIN HOLDER
Dimensional analysis
FLYER AND SPINDLES
Dimensional analysis, Hardness, Eccentricity, Static balance
WEFT PIRNS
Dimensional analysis, Eccentricity
SITRA is a pioneer textile research association in the country with support offered by the Ministry of textiles, Government of India and the industry, offering multiple services like testing, calibration, energy audits, technical consultancies, training, etc.
The awareness on quality of products and services has grown manifold over the years on the industrial front as well as on the domestic front. The demand for quality products has increased to a great extent in spite of the higher cost, since a quality product scores over a cheaper competitor in the long run.
To continuously monitor the quality parameters right from raw material to delivery of the finished goods, an assortment of instruments are used by the industry. These instruments have to be accurate enough to measure the quality parameters of the materials or the tools and devices. In many instances these instruments are used routinely without taking into consideration the errors present in the instruments.
The accuracy of the instruments used in the organization should be periodically checked against a standard equipment to ascertain whether the deviations or errors in the instrument are within specified tolerances.
Necessity for Calibration of instruments
Like all other equipment, Measurement and Test Equipment are not ideal since they have inherent error elements. The Measurement and Test Equipment cannot caution the user as to when the instrument is operating out of its specified tolerance levels. Only a major malfunction is visible to the user and only a technically well-equipped calibration facility can determine the actual performance of the instrument and the associated deviations in the Measurement and Test Equipment.
The amount of error in an instrument can be determined by calibrating the instrument periodically. Calibration is the process of comparing the instrument under consideration with a standard reference equipment having Traceability to National or International Standards. Calibration of an instrument throws light on the quantum of error present in the instrument and its suitability for usage in the quality system. Depending upon the quantum of error, the instrument is set right by adjusting necessary settings and fine-tuning the instrument. If the quantum of error goes beyond standard tolerance levels, then the instrument should be prohibited from usage until the error is rectified and the deviations are minimized to tolerable limits.
SITRA has been offering calibration services for textile testing & measuring instruments for the past three decades. Calibration services are offered for instruments and testing machines used in spinning, knitting, processing and garmenting industries.
Many textile mills in Coimbatore, Tirupur, Salem, and neighbouring states have been regularly availing SITRA’s calibration services for a variety of instruments. SITRA calibration certificates are accepted by ISO 9000, ISO 14000 certifying authorities.
Our calibration laboratory has got accreditation from National Accreditation Board for Testing and Calibration Laboratories (NABL), in accordance with ISO/IEC 17025:2017, for Mechanical, thermal and Electro technical calibrations (Accreditation certificate no. CC-2678) for the following parameters:
- Dimensions
- Volume
- Temperature
- Specific heat and Humidity
- Timer
- Temperature simulation
- Pressure & vacuum
- Speed
- Weights
- Weighing balances
- Force – Tensile testing
Please find attached herewith a copy of SITRA's Certificate of Accreditation and the second file providing details of our calibration services.
We are happy to share the above information with you and earnestly hope that you will utilize our services for your calibrations needs.
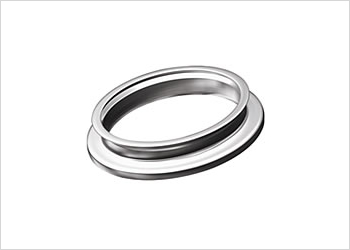

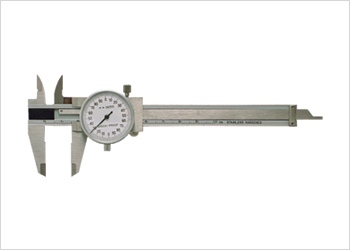
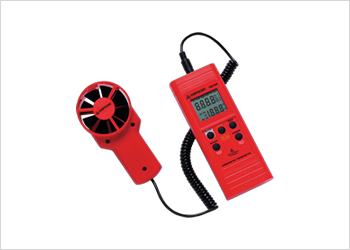
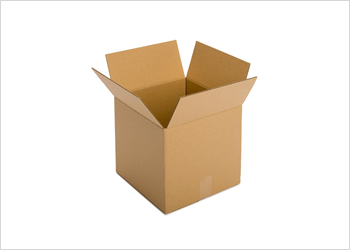

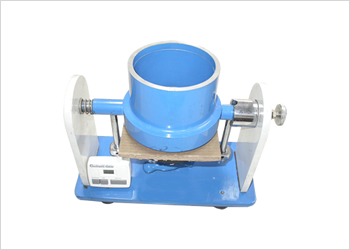
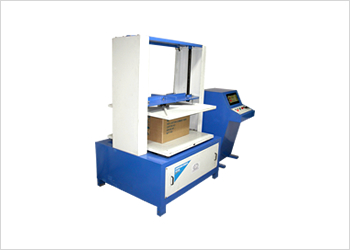
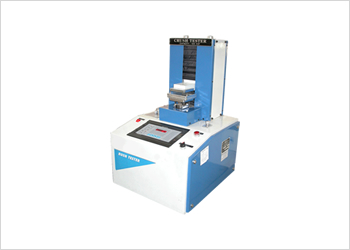
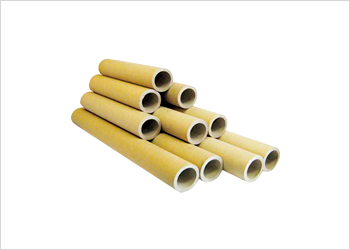
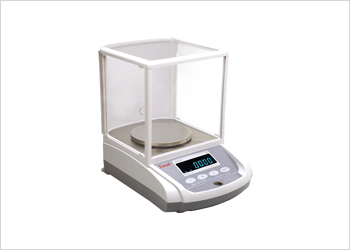
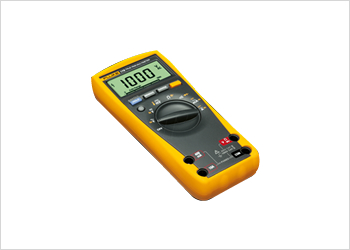
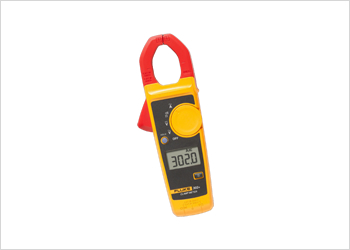
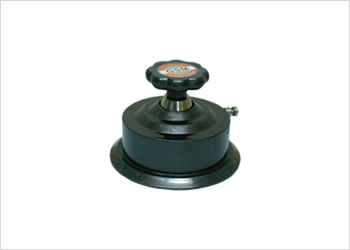
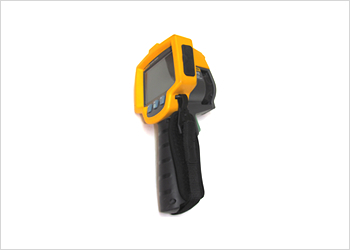
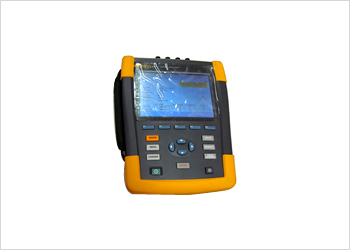
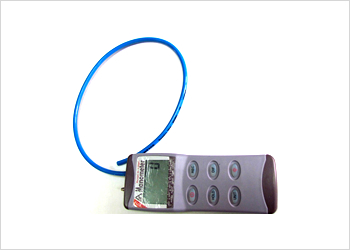
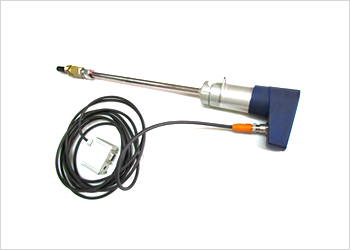
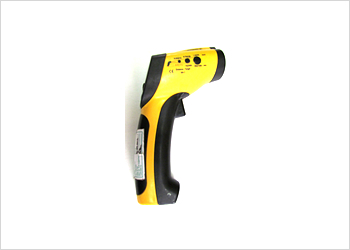
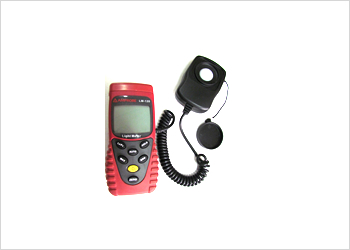

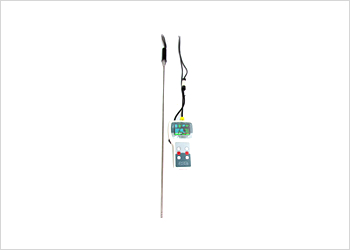
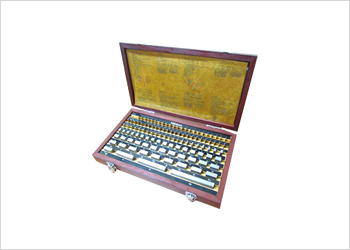
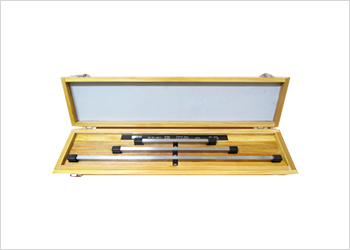
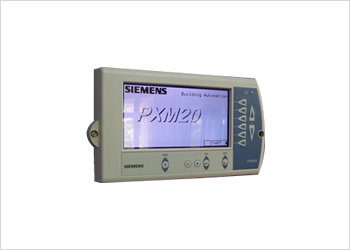
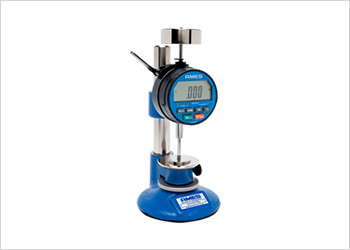
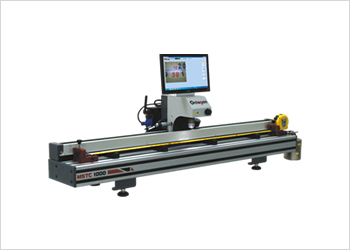
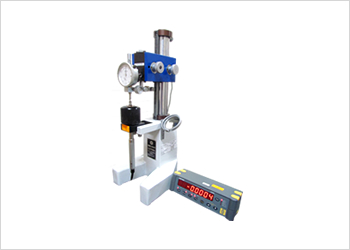
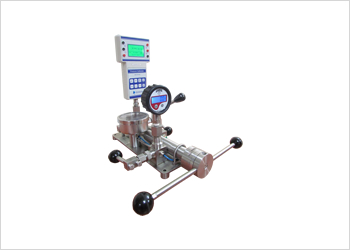
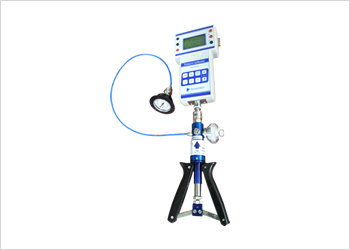
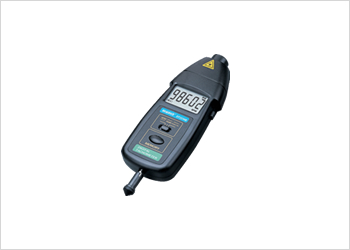
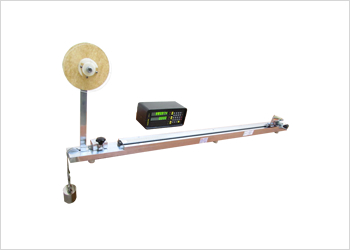
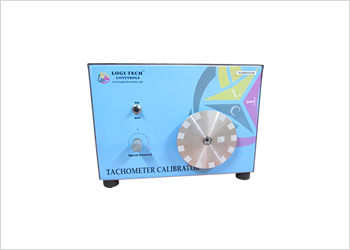
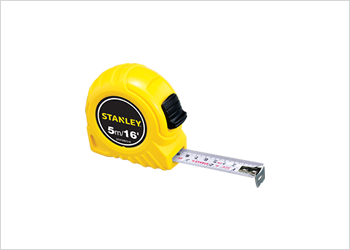

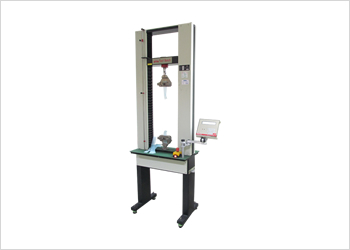